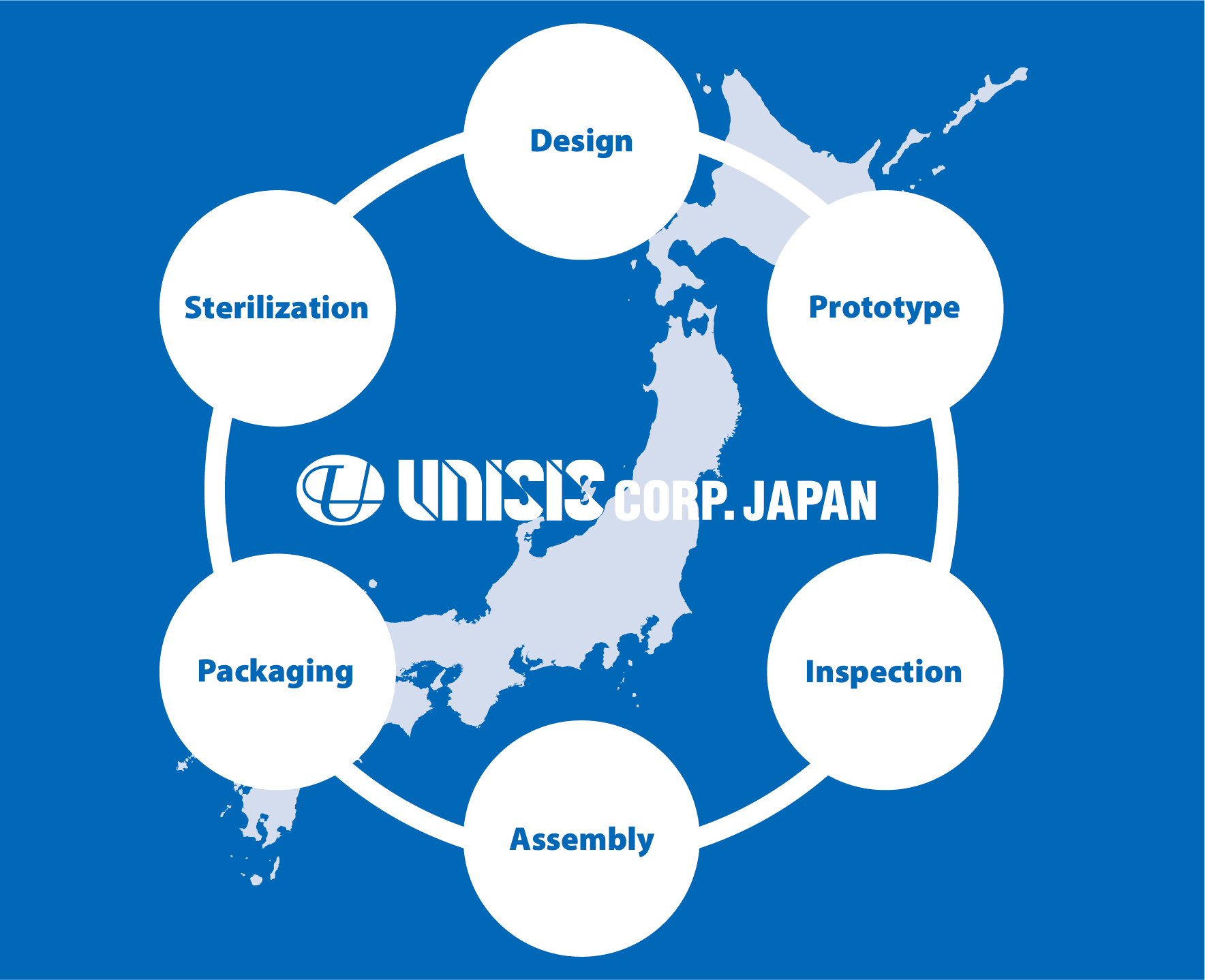
What UNISIS ?
-
1
''Integrated manufacturing' of medical devices from design to assembly and packaging to sterilisation
-
2
Experiences on obtaining Japanese/overseas regulatory authorization(CE certification, US FDA 510k, ANVISA, KFDA etc)
-
3
Export our products to 50 countries worldwide.(our branded products and OEM products)
FEATURES OF UNISIS
We own a variety of equipment to meet a wide range of customer needs.
In addition, the various types of equipment as well as skilled technology enable the production of high-quality products.
PRODUCT REALIZATIONORDER TO DELIVERY

Please send your inquiry to us by email or fax if you are interested in our products.
You can call us directly, but the person in charge may not be available because of the time difference.

The person in charge contacts you in response to your inquiry.
The following information may be required:
1. Company name, address, and name of person in charge of your company. If we have an agent in your country, there is a possibility that we introduce our agent.
2. Product name. If unknown, please specify the intended use of the product. We will reply to you with information about our relevant product for the same intended use.
3. Product specifications (gauge size, length, packaging, and required labeling etc.)
4. Intended use or purpose (detailed information is required when the product is a non-standard product or intended for a special use).
5. Quantity and delivery request
6. Request for samples, if any.

Our RD and QA team investigate the technical and/or regulatory requirements of the product as necessary.
When your required product is new to us, we conceive and provide a new design drawing based on the specifications.
We inform you of a rough cost estimation.

We receive your aproval of the design, drawing, specification and the quotation.At the same time, we discuss the terms and conditions with you, which will be reflected to our Proforma Invoice.

Samples of existing / new models are provided upon request.
Prototypes are manufactured for new models.
Samples of existing models are provided for evaluation.
* The samples of existing models may be shipped during Step 3 or 4 above.

The product specifications are confirmed with your approval for the specification and/or evaluation of the samples submitted.
At this point, we provide you with the final price.

Upon receiving the formal purchase order, we issue the corresponding proforma invoice.
Our proforma invoice is to re-confirm your order contents(item, quantity, delivery) and also the terms and conditions set in Step 4.

Your order will be carefully manufactured at our plant in Japan. Products only which have passed our strict quality inspection will be released for delivery. We package and sterilize the products in our plant/sterilization center when the individualy package and sterilization is required.
* Some items may be produced and sterilized at our partner plants under our strict control.

We will inform you of of our delivery plan in advance so that you can arrange the payment.
Upon receipt of your payment, we prepare the shipping documents and arrange the freight forwarder.

The finished products will be shipped via air or sea freight to you.
From the medical field to a wide range of industries, we offer needle tip shapes and processing technologies to meet customer requirements.
Various needle tip shapes are presented here.
LANCET POINT
Widely used, such as hypodermic needles, tip shape of minimum pain
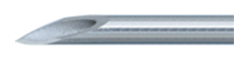
K-3 LANCET POINT
Classic tip shape for spinal needles, with firm puncture feedback
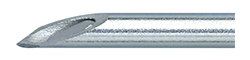
PENCIL POINT
Minimally invasive pencil-shaped tip with a hole on the side
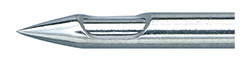
HUBER POINT
Curved tip towards cutting face
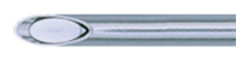
CRAWFORD POINT
Ultra short bevel with large-angled cutting face, mainly used for caudal anesthesia
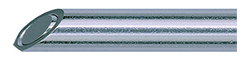
LUTZ POINT
Round tip with a hole on the side to minimize damage to tissue
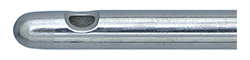
BACK CUT POINT
Cutting faces on both sides of the back of the main cutting face for smooth insertion
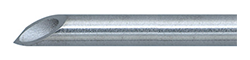
TRI-BEVEL POINT
Sharp triangle cutting face, mainly used for vessel puncture
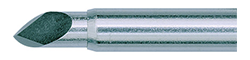
WESCOTT NEEDLE
Developed for lung biopsy, efficiently collect tissue even with a thinner gauge
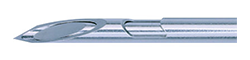
BLUNT TIP NEEDLE
No cutting face with a tapered tip for blunt puncture
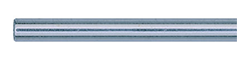
FRANSEEN NEEDLE
Sharp trigonal shape, optimal for biopsy of relatively firmer tissues
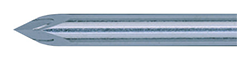
BULB HEAD NEEDLE
Minimizing the tissue damage in treatments such as vasodilation
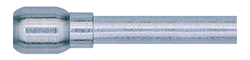
MADAYAG NEEDLE
Sharp conical tip stylet for smooth insertion, optimal for deep tissue biopsy
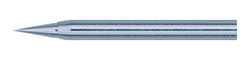
OTHER UNIQUE SHAPES
Unisis offers tailor-made tip and surface treatment

HOLE
Desired location and size. Ex Spiral, penetration
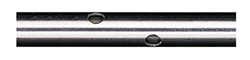
ENGRAVING
Engraving on the side of needles for echogenicity. Our advanced quality management allows both clear visibility and smooth insertion
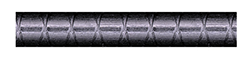
MARKING
Electrolytic etching for depth marking. We offer a wide range of patterns at your request.
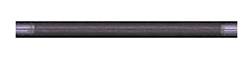
CHAMFERING
Treatment to round the edge of the needle, for the purposes of minimizing damage on the tissues and manufacturing defects
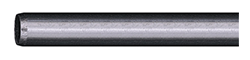
SWAGING
Narrowing gradually towards the end of a tube
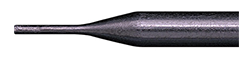
SHOTBLASTING
Glass beads or sand are applied on the surface to roughen or modify.
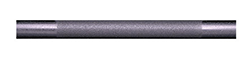
PRODUCTION WORKFLOW
STEP 01RECEIPT OF RAW MATERIAL
Stainless steel tubing & wire, plastic components, and packaging materials are delivered by our suppliers in Japan.
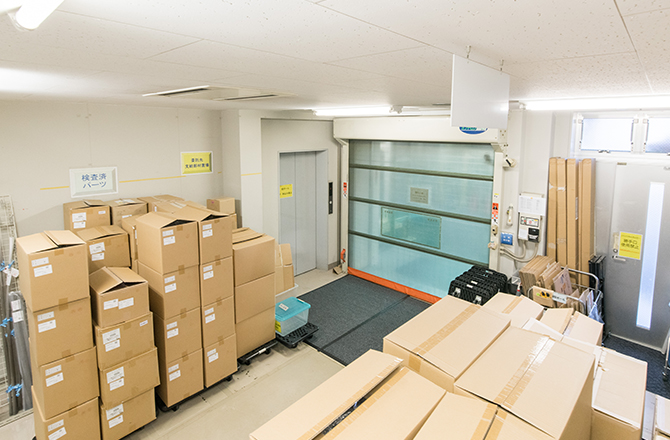
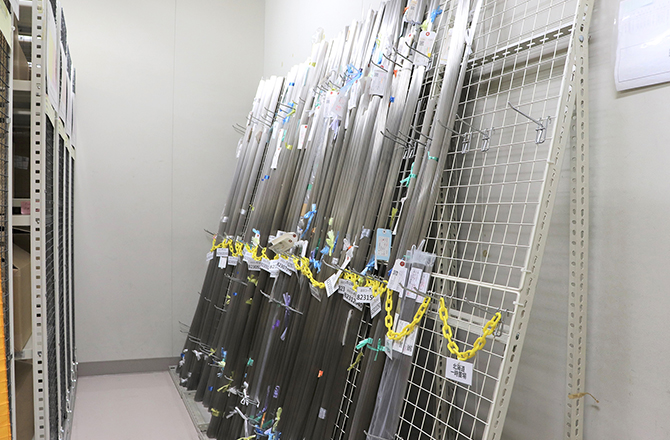
STEP 02CANNULA PRODUCTION
Stainless steel tubing is ground into cannulae, with precision and quality strictly overseen by skilled staff online.
Finished cannulae are washed with purified water in the cleanroom.
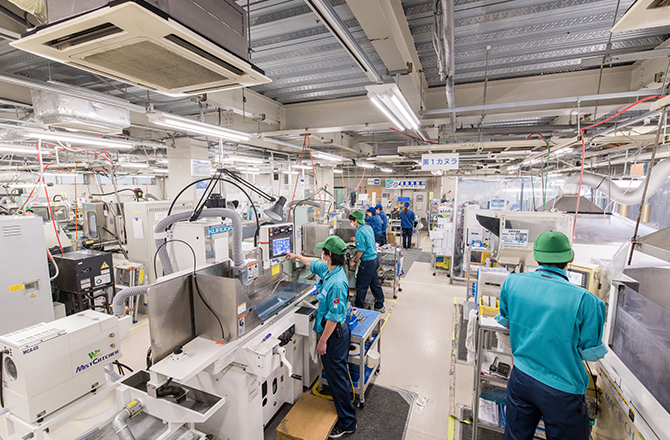
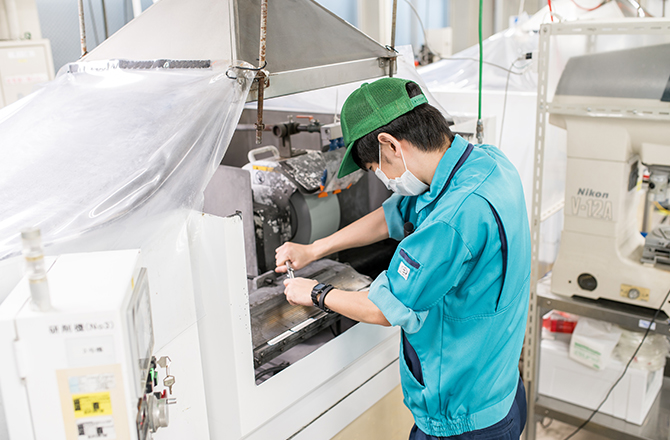
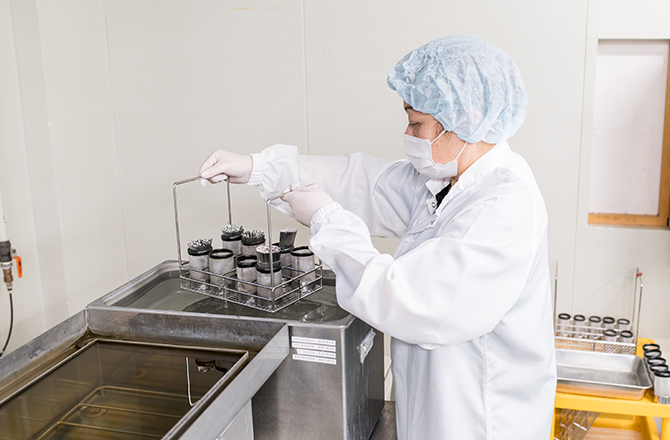
STEP 03INSPECTION
Cannulae and other components are inspected mechanically and visually.
Because we produce a wide variety of products in small quantity, inspection is hardly automated. Most needles are visually inspected.
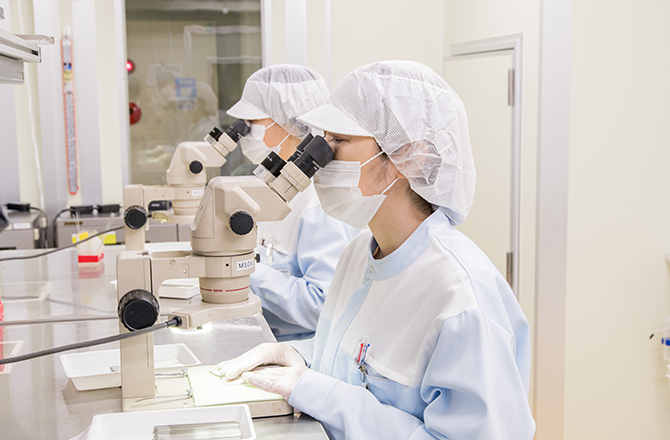
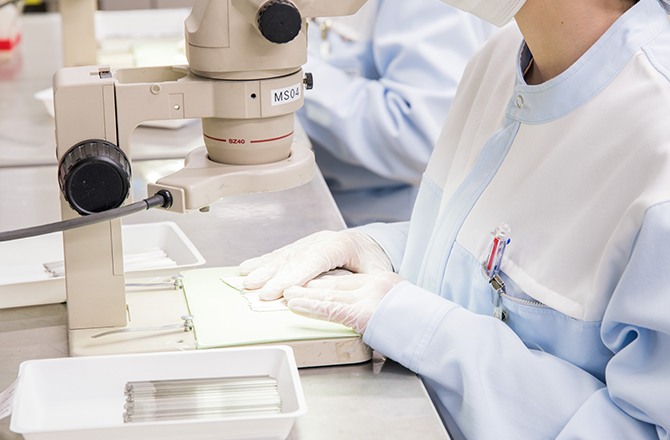
STEP 04ASSEMBLY
Assembly is performed in clean (CLASS 10000) rooms. Manual assembly of a wide variety of items each in a small number requires skills of experienced assembly staff. The production process is continually updated, and the cell production method is currently the norm.
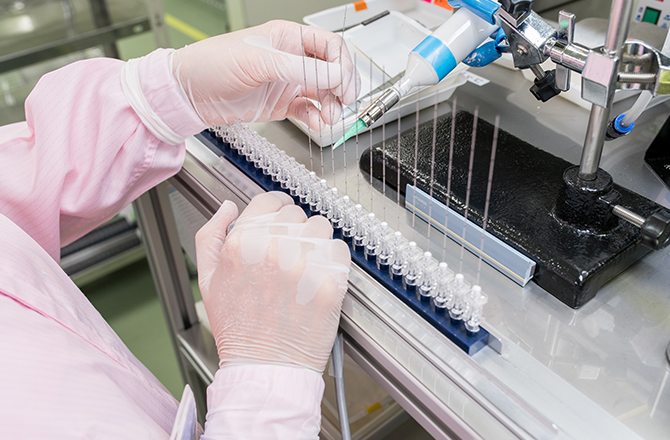
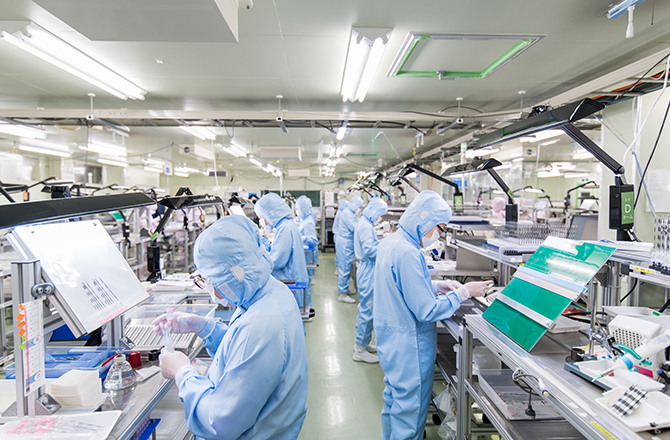
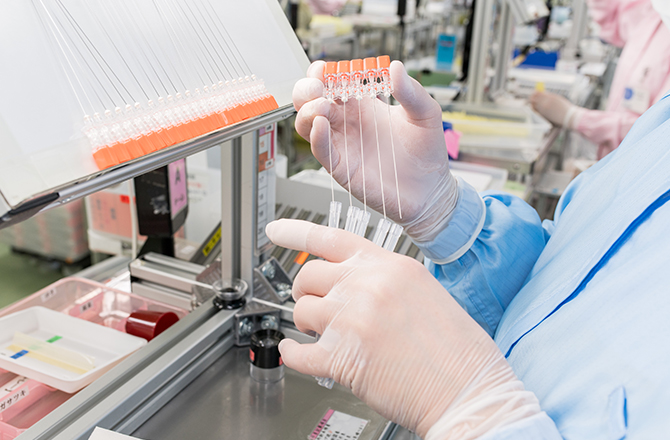
STEP 05PACKAGING
Finished products are packaged in a cleanroom equivalent to that for assembly.
An appropriate package(sterilization pouch, soft blister pack, etc.) is selected depending on the product.
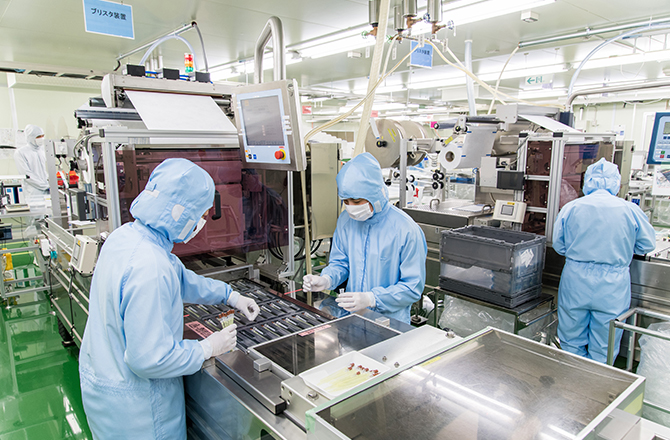
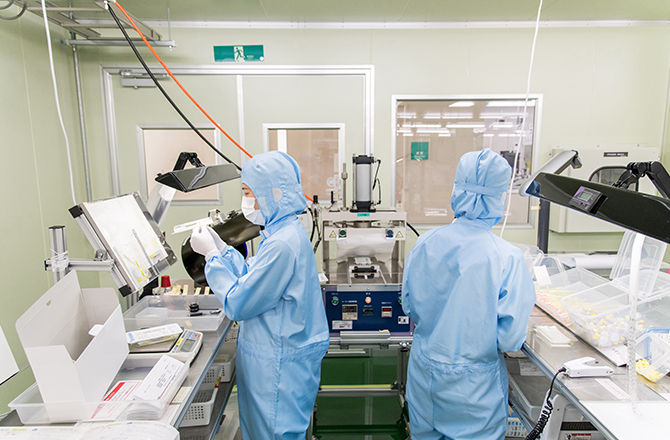
STEP 06STERILIZATION
The packaged products are sterilized in the sterilizer.
Unisis uses ethylene oxide gas(EOG) sterilizer to avoid effects on plastic parts.
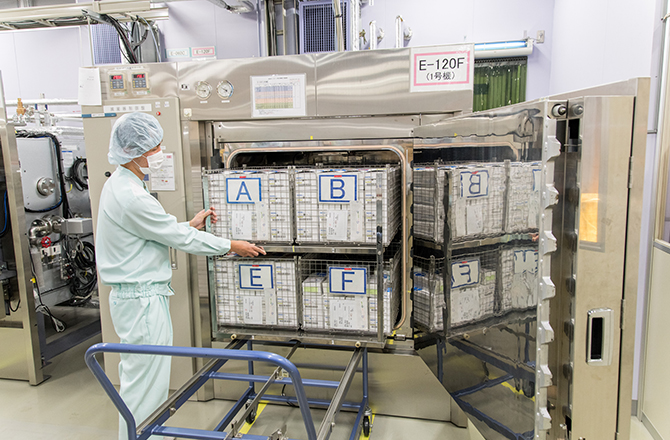
STEP 07PERFORMANCE TESTING
Our QA department performs random inspections, such as culture examinations, before shipment.

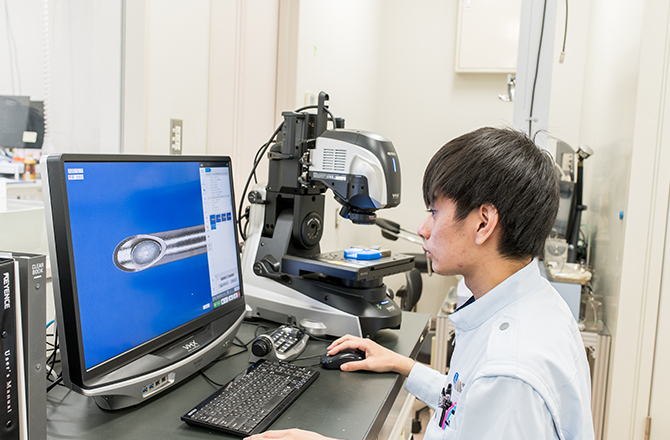
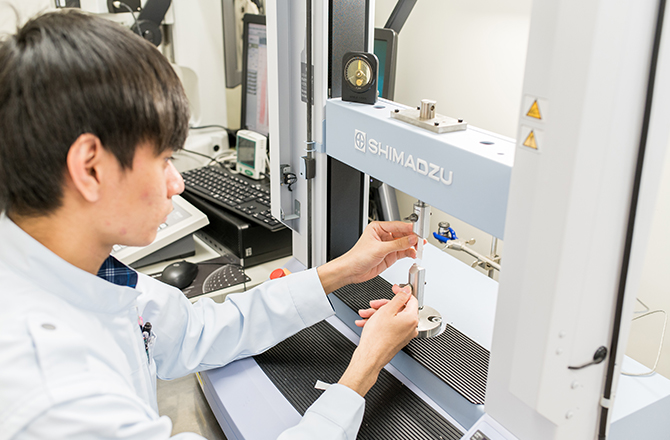
STEP 08SHIPMENT
Products that pass inspection are packed in double carton boxes to protect against damage and shipped to our customers around the world.
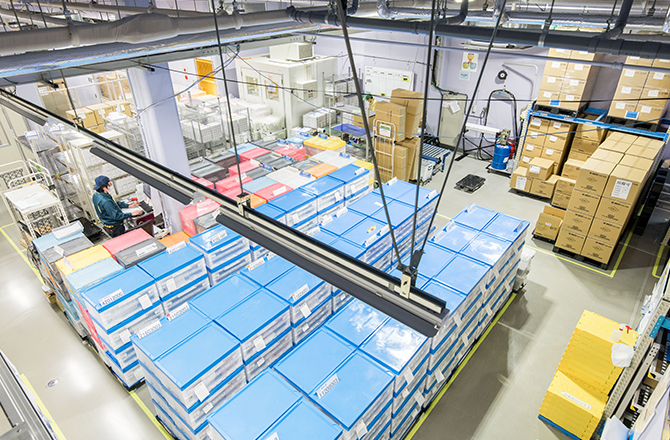
How can we collaborate with your business?
・You have technological foundation in manufacturing, but no license to launch as a medical deivce
・You have an idea that could be applied to a medical device, but too challenging to develop it
・You do not have a facility to mass-produce a developed product (assembly, packaging, sterilization etc.)